Pioneering Projects: Shaping the Future of Manufacturing
In this dynamic space, you’ll discover the diverse array of projects undertaken by our talented researchers, students, and collaborators. These projects encompass a wide spectrum of topics, from advanced materials development to AI-driven process optimization, all aimed at addressing the challenges of the modern industrial world.
Join us as we explore these transformative projects, each one a testament to our commitment to excellence, innovation, and impact. Whether you’re an industry partner seeking collaboration, a fellow researcher looking for inspiration, or simply curious about the forefront of manufacturing technology, you’ll find a wealth of knowledge and potential within our projects.
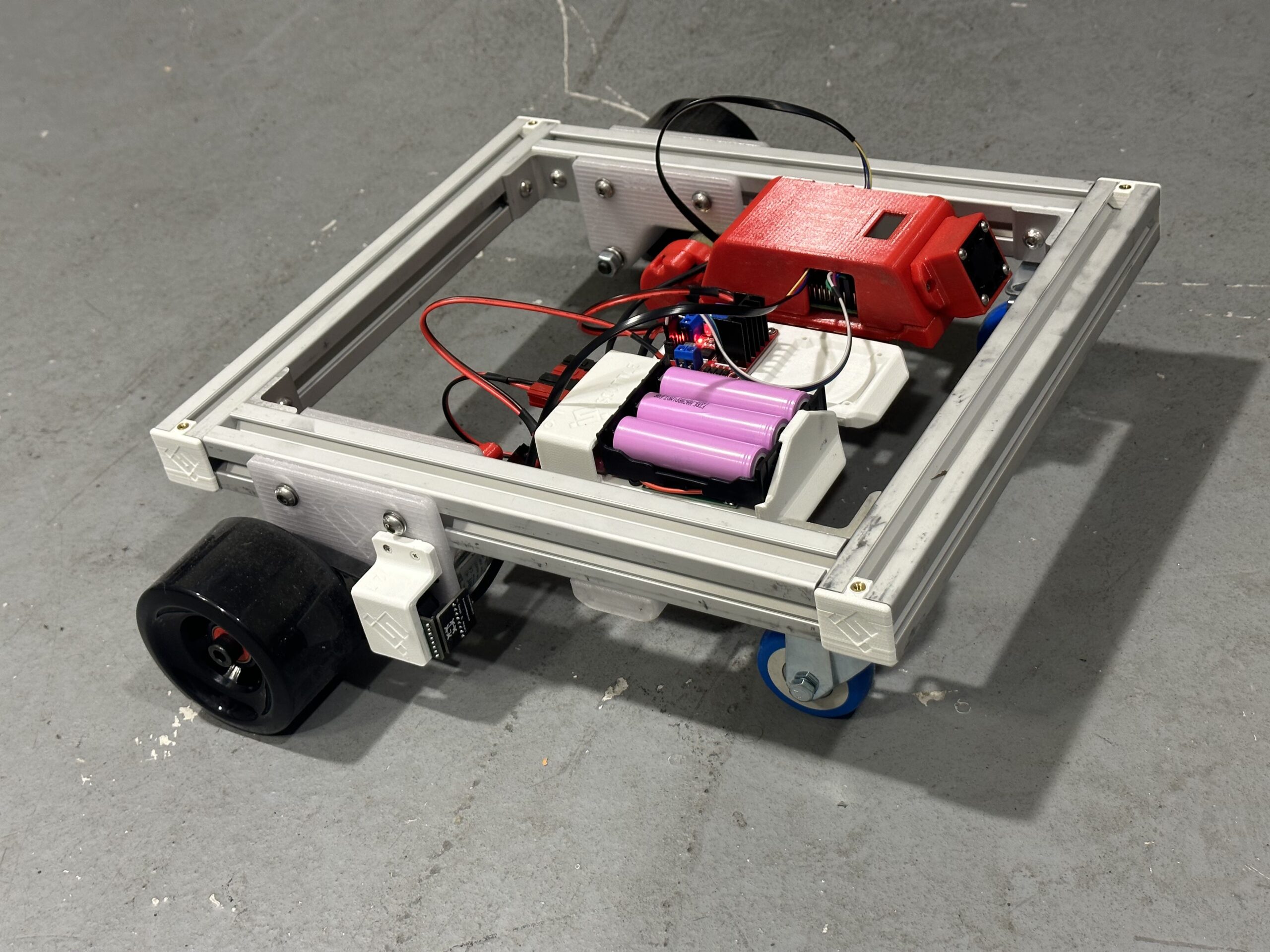
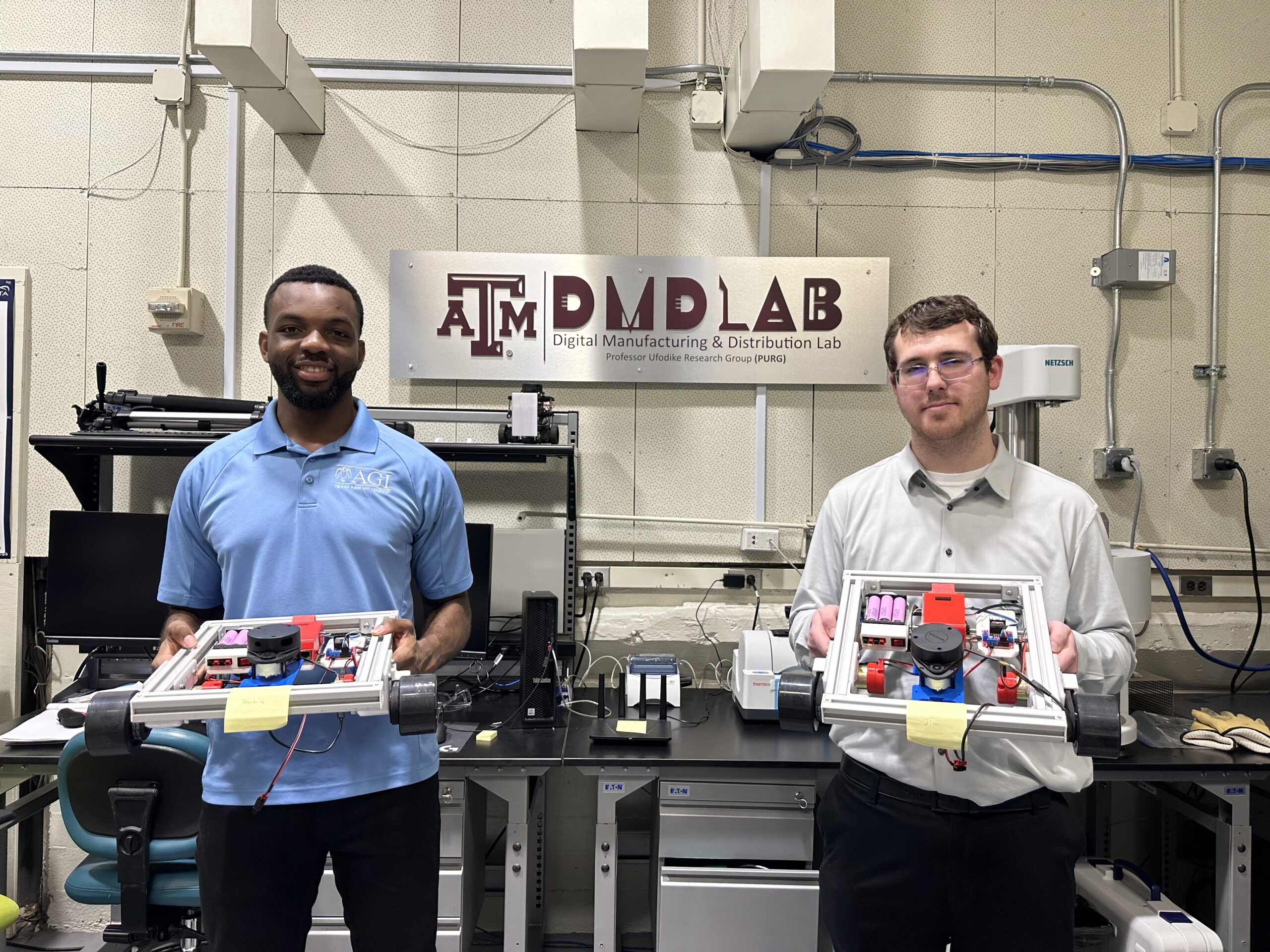
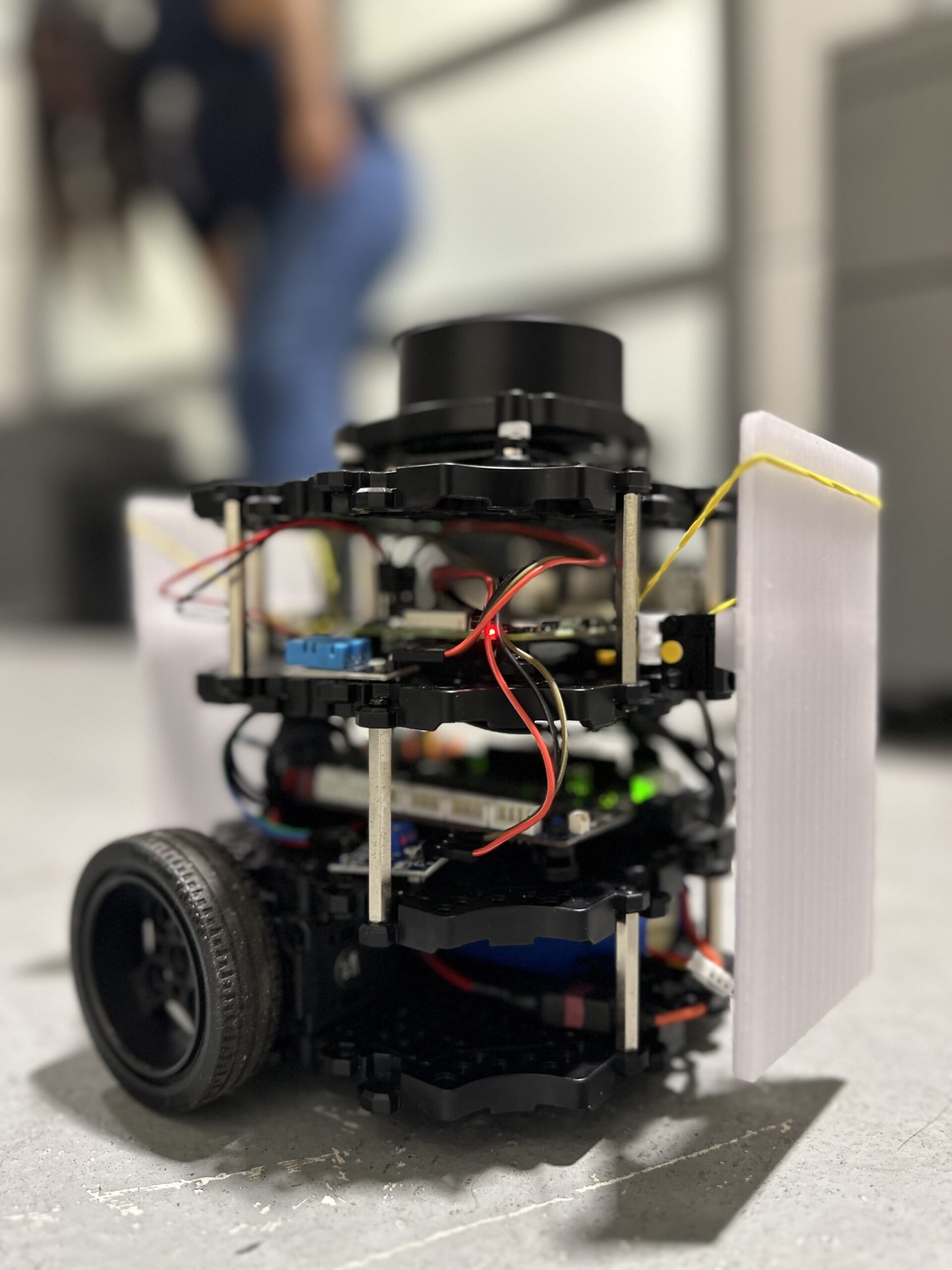
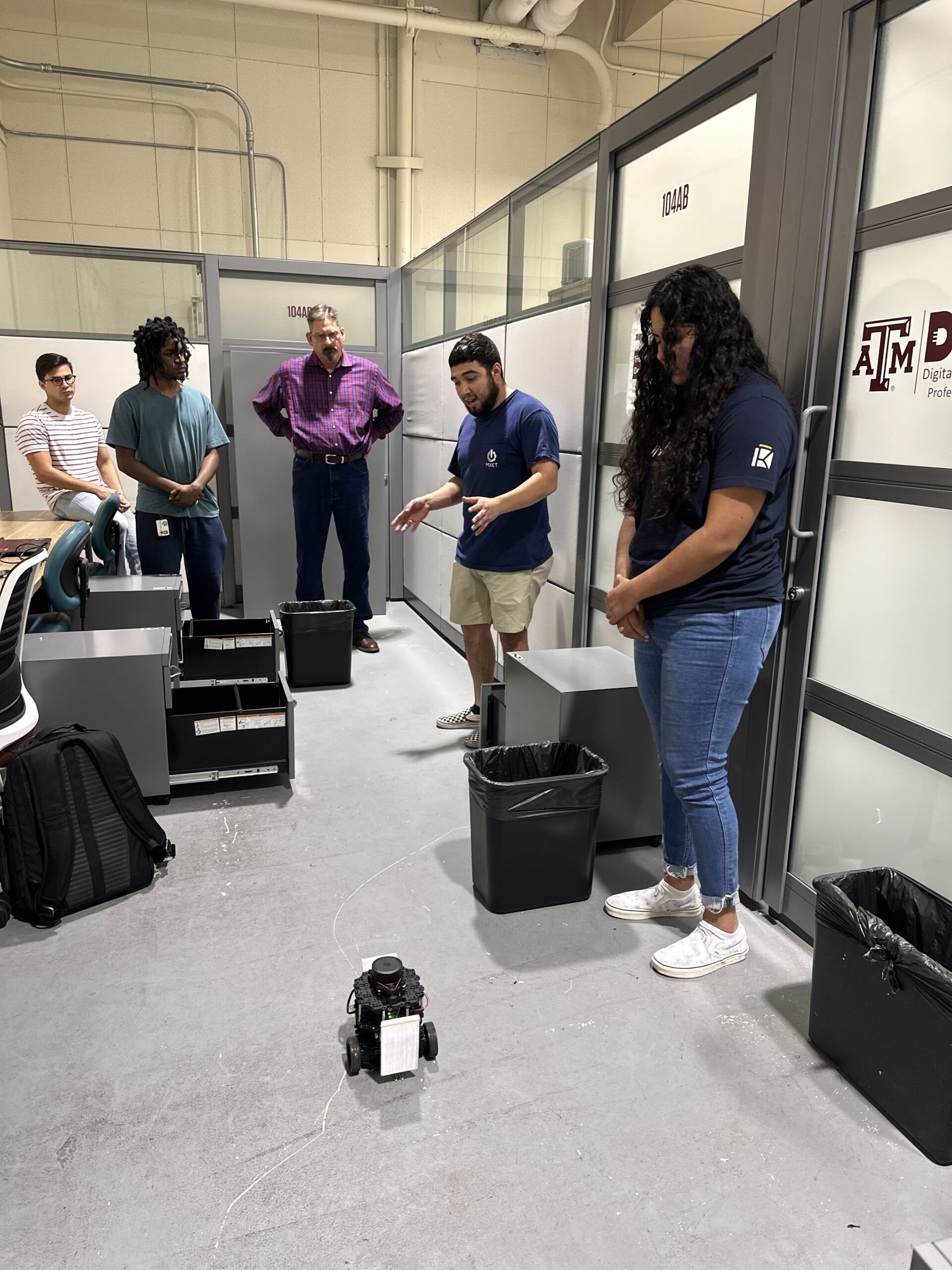
Custom EV Design and Manufacturing
In the current and continuously changing world we see the development and implementation of alternative sources of clean energy. This change has been greatly seen in many applications used in our everyday life. Most likely the greatest change has been in our transportation. With the development of electric vehicles, they are gradually becoming the new method of transportation, reducing the amount of CO2 emissions every year. To adapt to this change, more internal combustion (IC) vehicles are being electrified.
This project involves the electrification of motorcycles. While there are electric motorcycles on the market, they are very expensive, don’t provide as long a driving range as IC motorcycles, and are generally much heavier. Within this project, the overall goal is to design and manufacture an electric motorcycle and identify the points of cost reduction, weight, and extended range. To do this, an electric motorcycle will go through different phases and design/manufacturing aspects.
The motor controller, a Kelly KLS96601-8080IPS, is rated for 96V with 240A of continuous current. The accumulator is the heaviest part of the motorcycle. To reduce the weight as much as possible, the material used as the container is 6061-T6 aluminium. Because it is a soft metal, multiple FEAs must be run to determine the appropriate thickness. When building the battery pack, after determining the most optimal battery type, packaging, and energy output, the selected batteries were 18650 cells in a 27s16p configuration. This creates a 40Ah pack consisting of 432 cells. Attached to the side of the container, is the battery management system (BMS). The selected BMS allows for multiple series connected and up to 300A of discharge current.
This project is not to immediately fix these three issues but analyze and make remakes of what to change for future manufacturers of electric vehicles. This motorcycle will use a hub motor rather than a traditional chain driven power transmission. It will also use additive manufacturing for complex designs and implement them correlating to the tires and other components. The chassis will go through different stages from being a ground-up manufacturing process to purchases to pre-built chassis to modify. Lastly the accumulator is designed to fit the maximum number of batteries while fitting the other required components in the chassis.
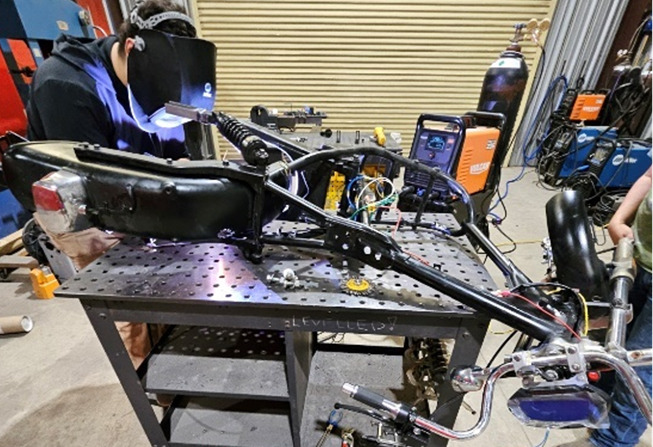
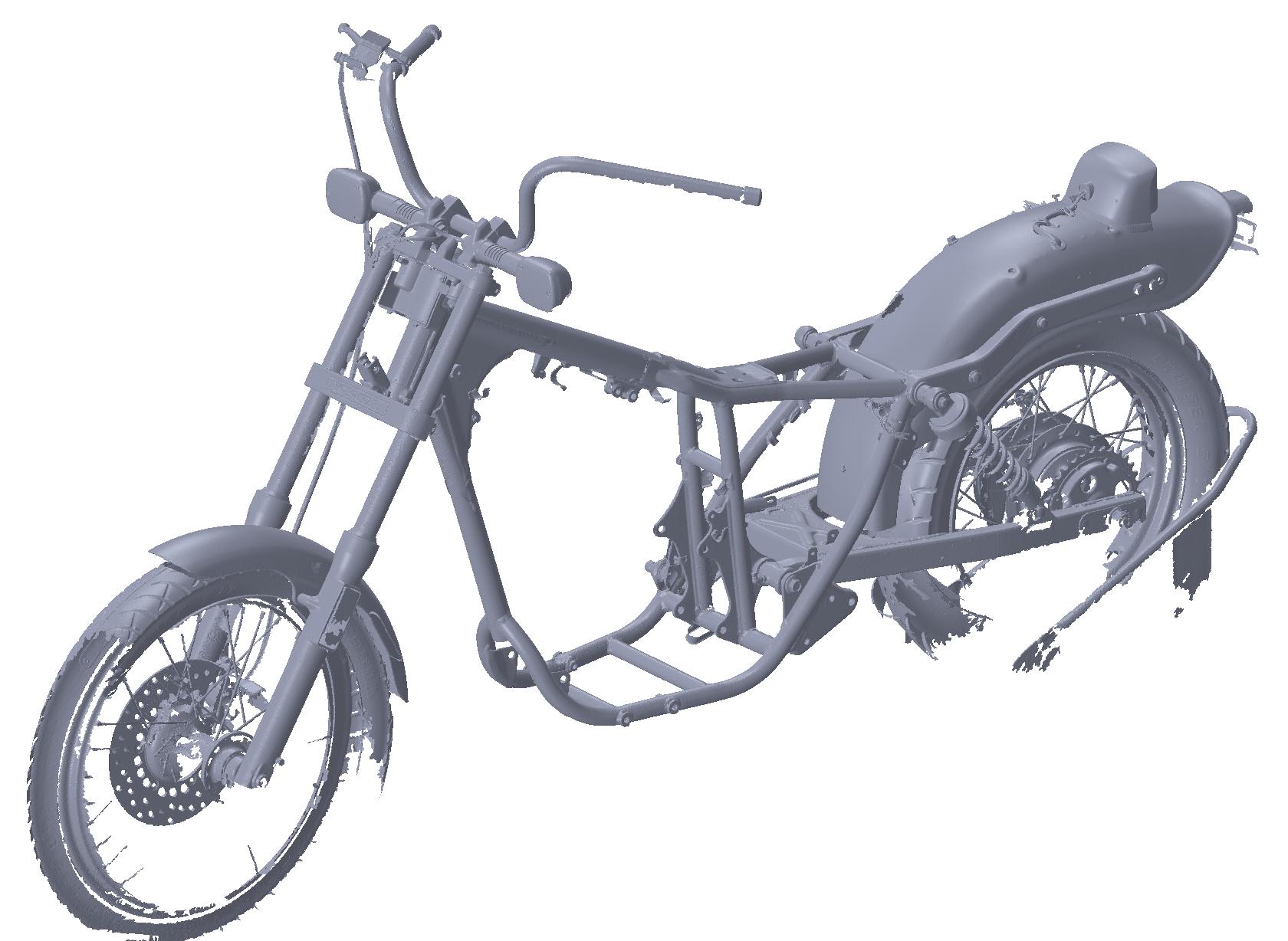
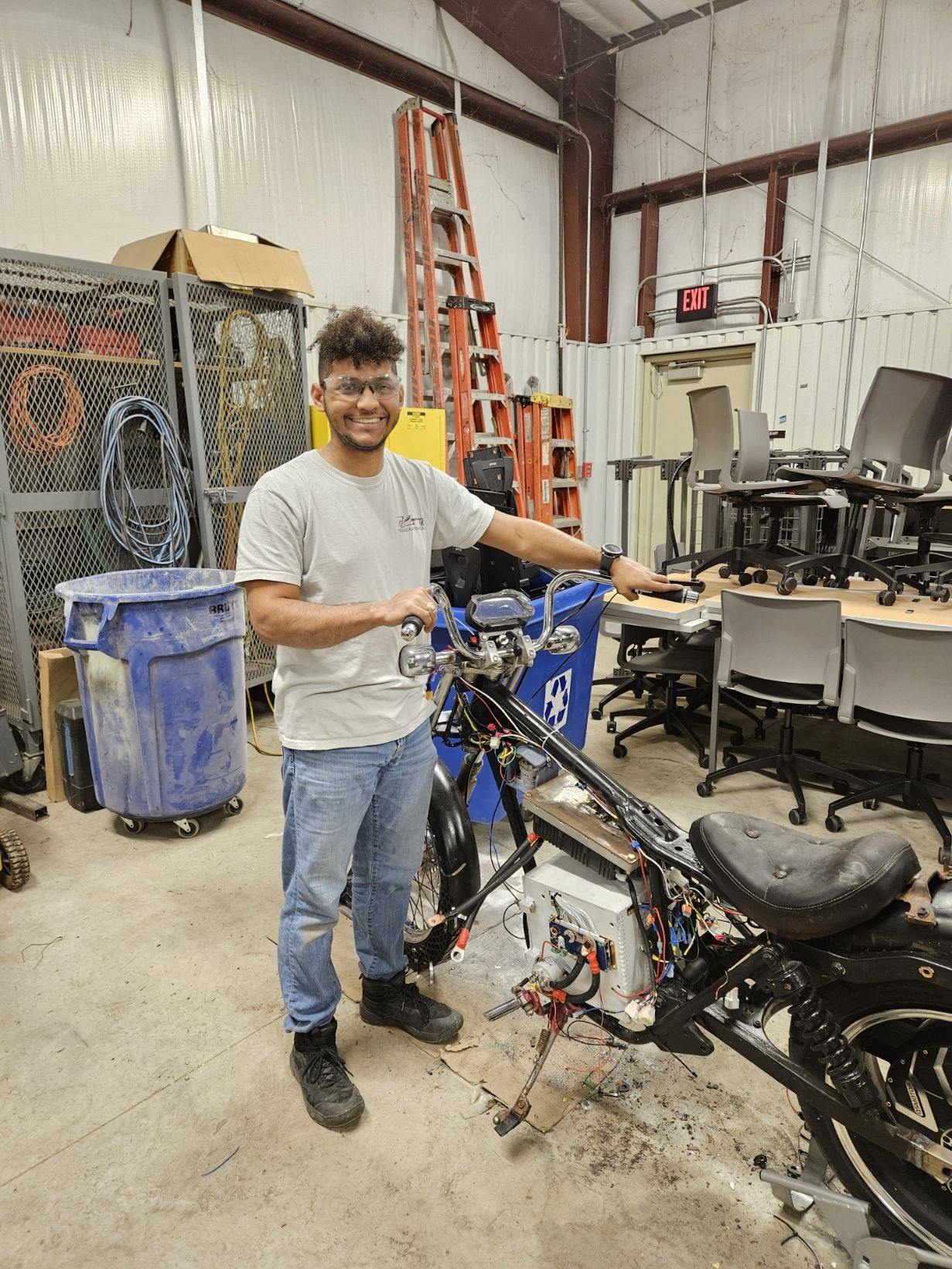
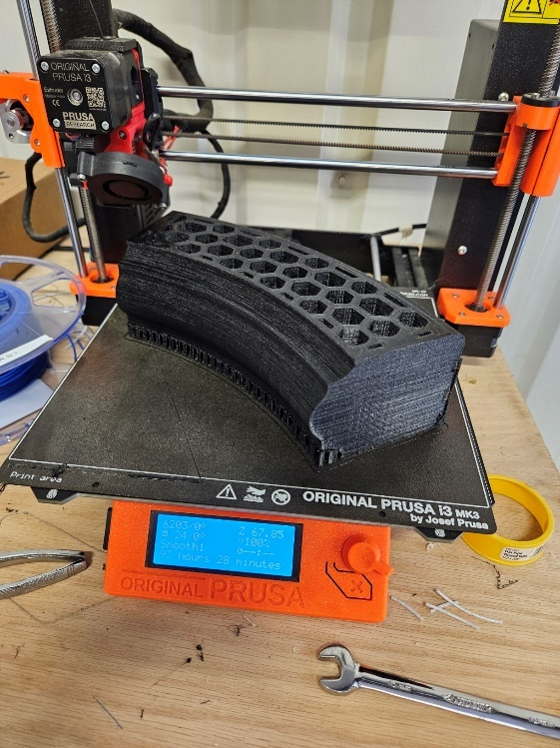